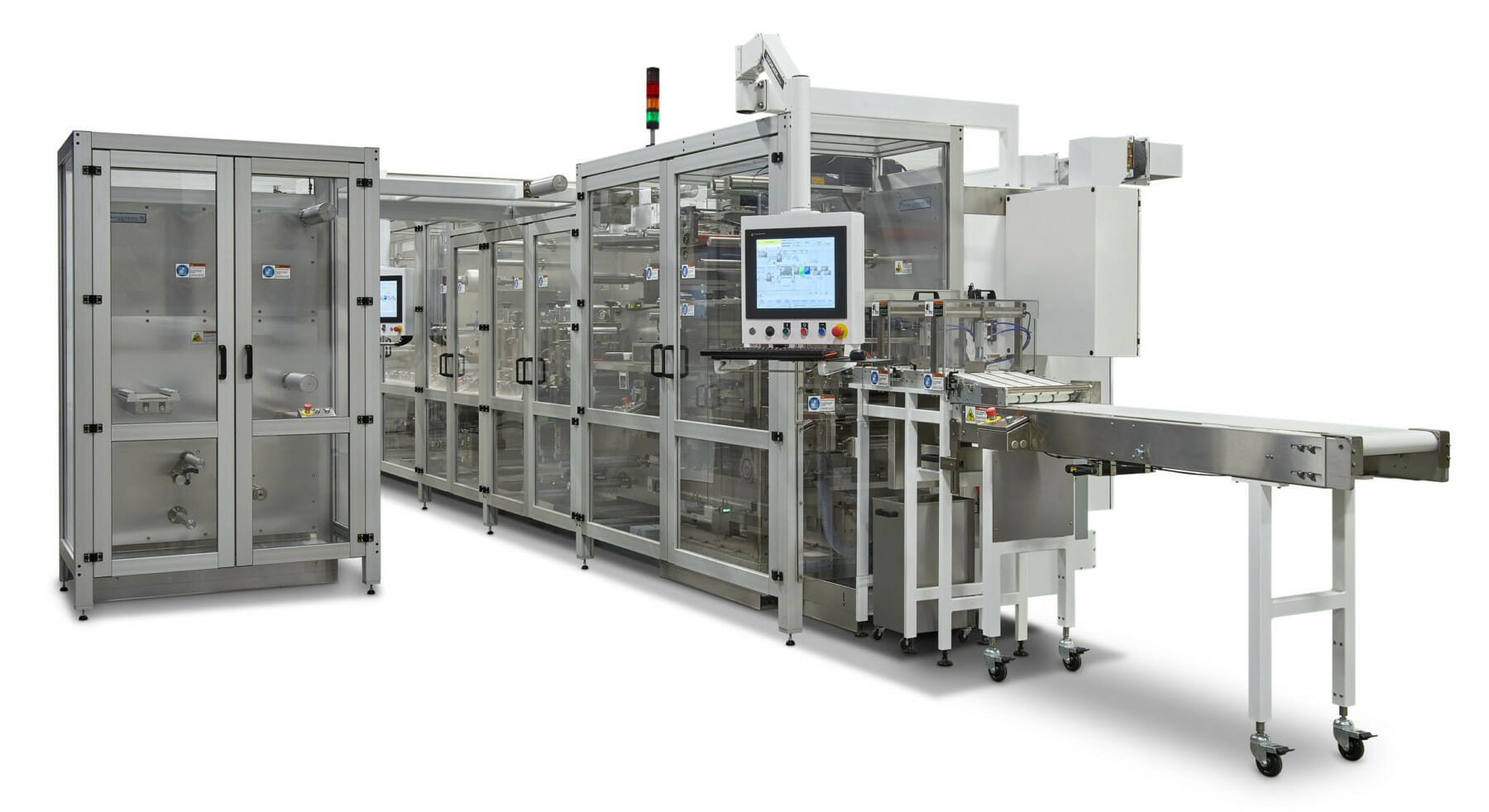
Transdermal Patch Manufacturing Equipment
Transdermal patch machines that ensure accurate drug dosage, maximize drug utilization, and provide inline quality verification for validated parts.
Transdermal delivery system designs that result in material savings of 10% to 50%.
Any transdermal patch manufacturer is faced with common challenges for assembling transdermal drug delivery system, including:
- Scrap reduction of expensive drug coated materials
- Precision of diecuts which directly affect product dosing
- Product inspection
- Lot/date code printing and verification
- End of line pouching
- Equipment and product validation
With a proven approach that has adapted to these and other challenges faced by transdermal patch manufacturers, we have a solution. Our solution to all these challenges is based on a modular transdermal machine that uses proven designs to mitigate risk. Because our cutting and placement methods are so precise, our clients have achieved material savings in the 10-50% range.
By integrating inspection, printing, packaging and robotics into our modular machines, we can move you from a 2-pass manufacturing approach to a 1-pass approach. A 1-pass approach from raw material to packaged transdermals will help you:
- Further reduce scrap,
- Mitigate material inspection, storage and movement issues (common with 2+ pass approaches).
- Assist in product validation – one machine and process to validate
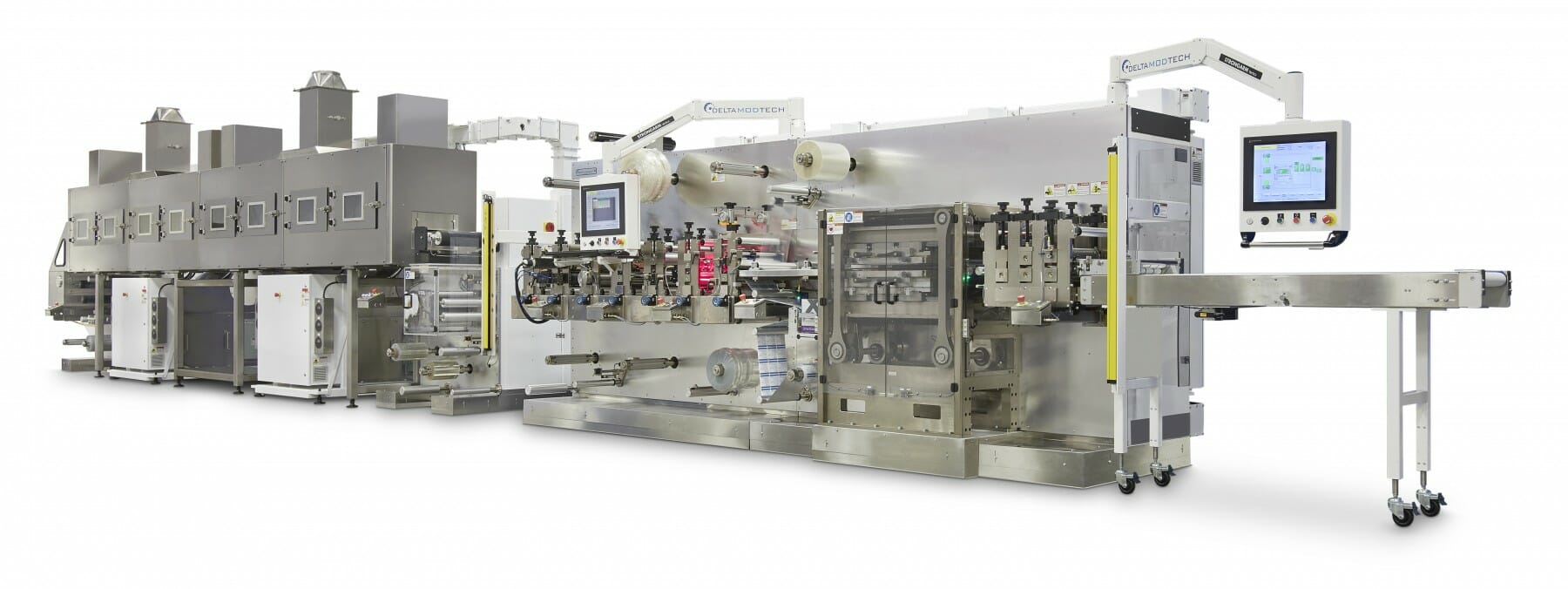
Machines that push the envelope for transdermal patch manufacturers.
Our machines are highly customizable for multiple product sizes and configurations.
Precise die cutting and placement technologies
Using our advanced die cutting and placement techniques, you can achieve smaller cuts with less scrap, maximizing your drug utilization. Additional scrap may be reduced by combining our die cutting modules with our inline MOD-TRACK™ Vision System to provide closed loop cutting corrections in real time.
Reject, shingling and stacking conveyors
Our conveying modules offer a variety of part handling functions and help ensure quality product verification. Part reject conveyors remove non-conforming parts with variety of lane options. Shingling and stacking conveyors allow for stacked parts with specific counts. Spreading and transfer conveyors are designed for process requirements.
Advanced tension control
Our advanced servo motor control allows precise tension control that can be perfected throughout the process to eliminate product curl.
Integration of end-of-line packaging and robotics
Masters in Motion® – Our team excels in the integration with OEM systems allow for complete automated manufacturing systems, controlled from one Touchscreen HMI.
Lot / date code printing
Seamless integration of OEM lot and date code printers that can be programed from your machines touchscreen interface.
Validation support for IQ/OQ/PQ
Accelerate your time to market! Utilize the experience of our validation team who are adept at working with our proven machine modules and a variety of converting processes. Our validation services are modeled after GAMP and allow the flexibility to work with you and your project needs.
Vision inspection of products
Our MOD-TRACK™ Vision System can be added to confirm product quality and update the registration position to assist in maintaining the best CPK for the process.
Heat-seal pouching
Our patented reciprocating heat seal technology allows for a repeatable seal time, temperature and pressure settings with continuous high speed motion.
CFR 21 Part 11 Compliance Tools
We are committed to delivering high quality systems that give customers the capability to comply with 21 CFR Part 11 and efficiently complete the validation of their machines.
The expertise behind the equipment.
These machines don’t design themselves. They also require the right training and support to ensure you’re running them at maximum efficiency. That’s why offer:
Application process and machine support
Keeping your machines running is priority #1. Most support can be done over the phone with an internet connection to the machine.
“Proof of principle” service for new products and processes
We can verify that the process / product can be produced within the customer specification.
Validation and documentation support
We can provide IQ/OQ/PQ support and custom documentation deliverables
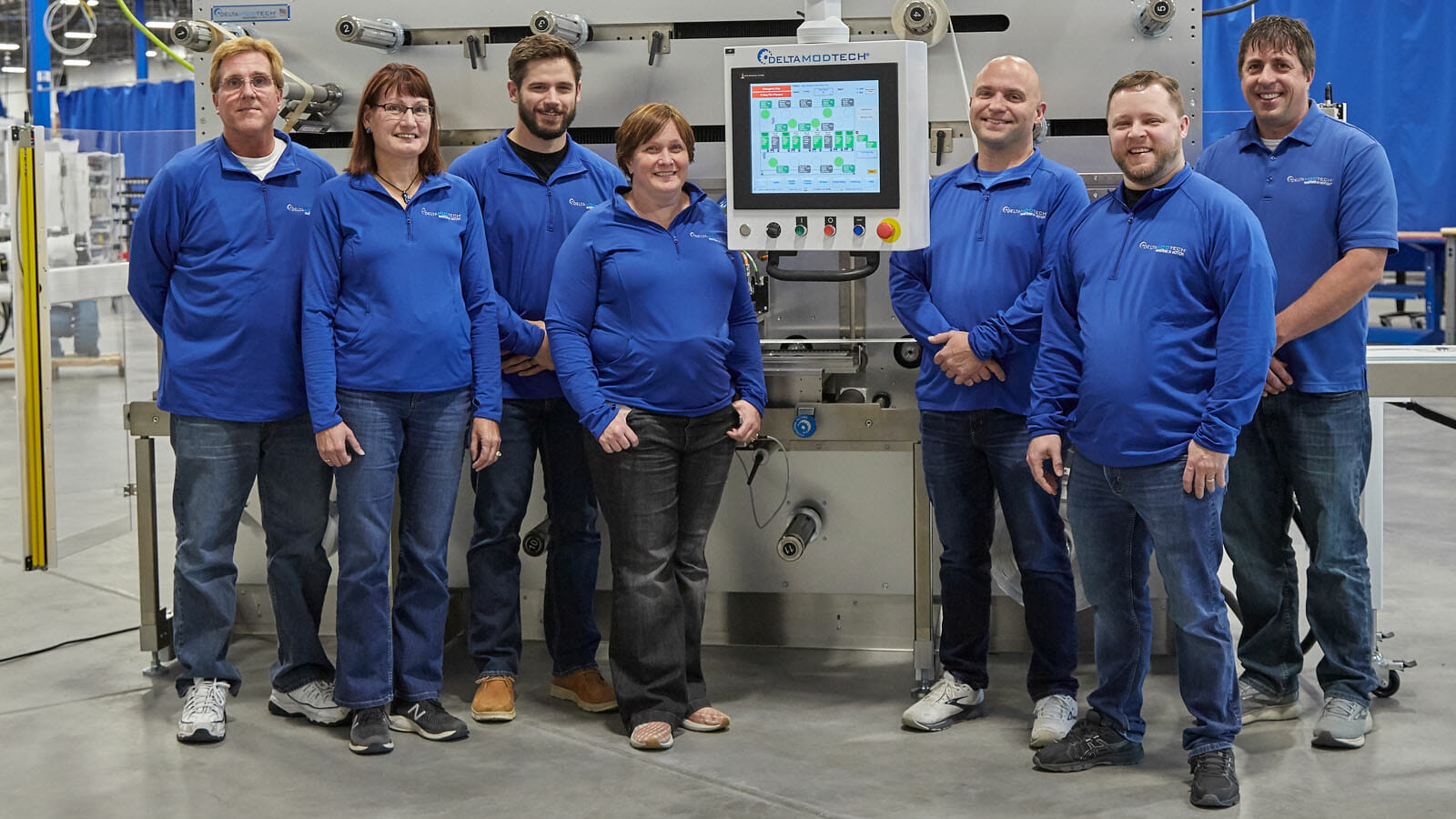
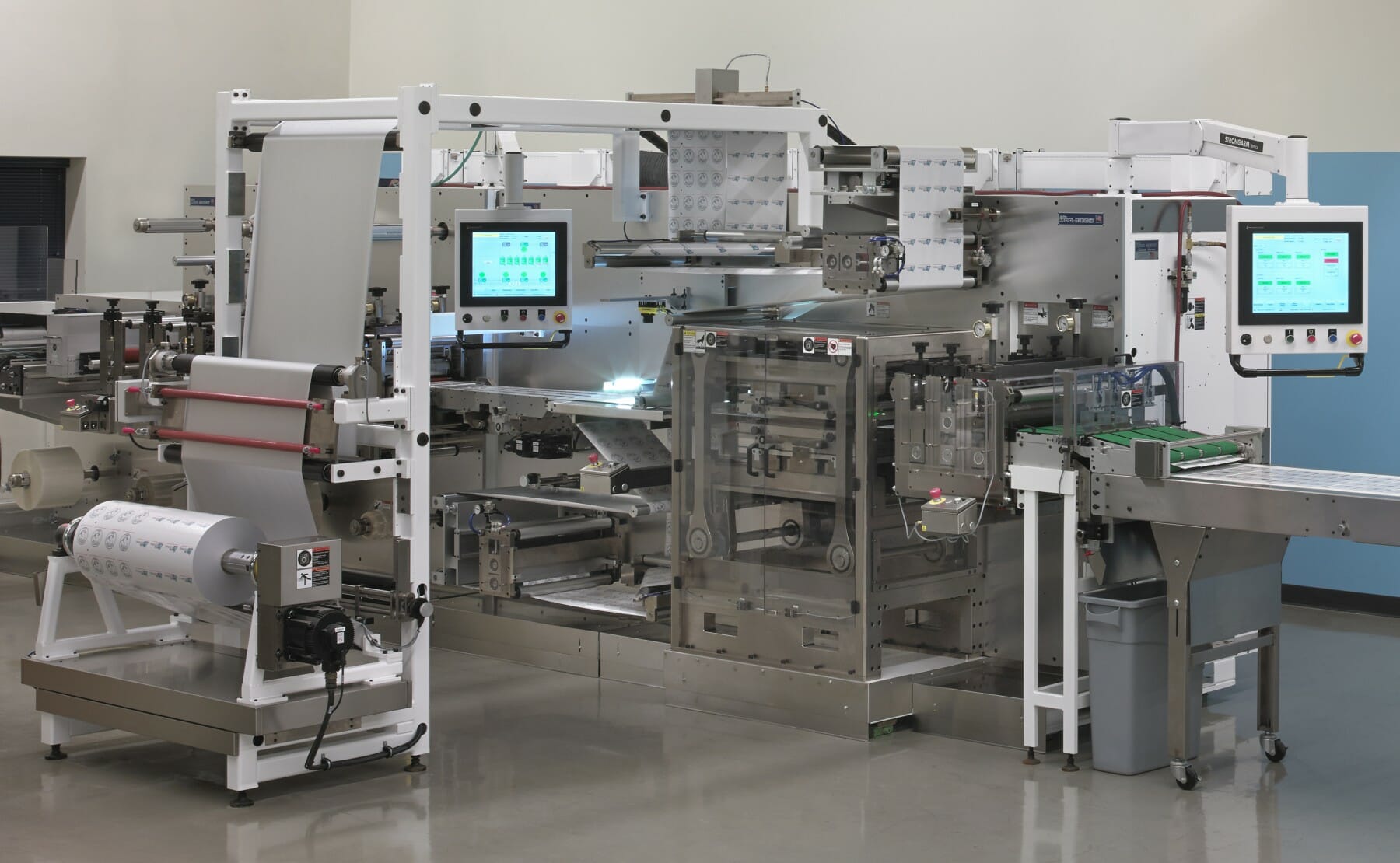
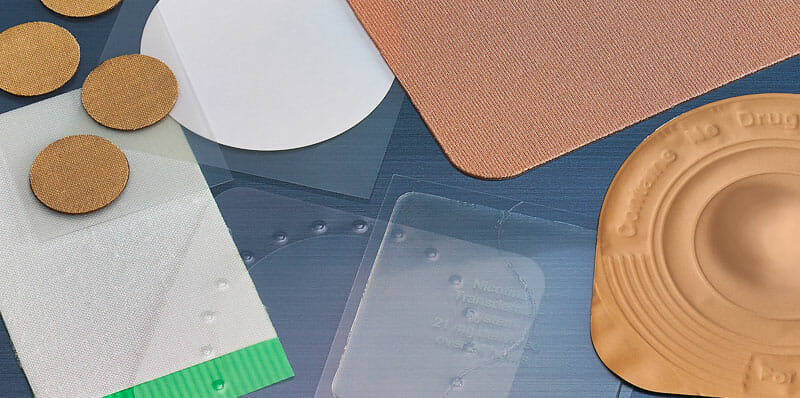
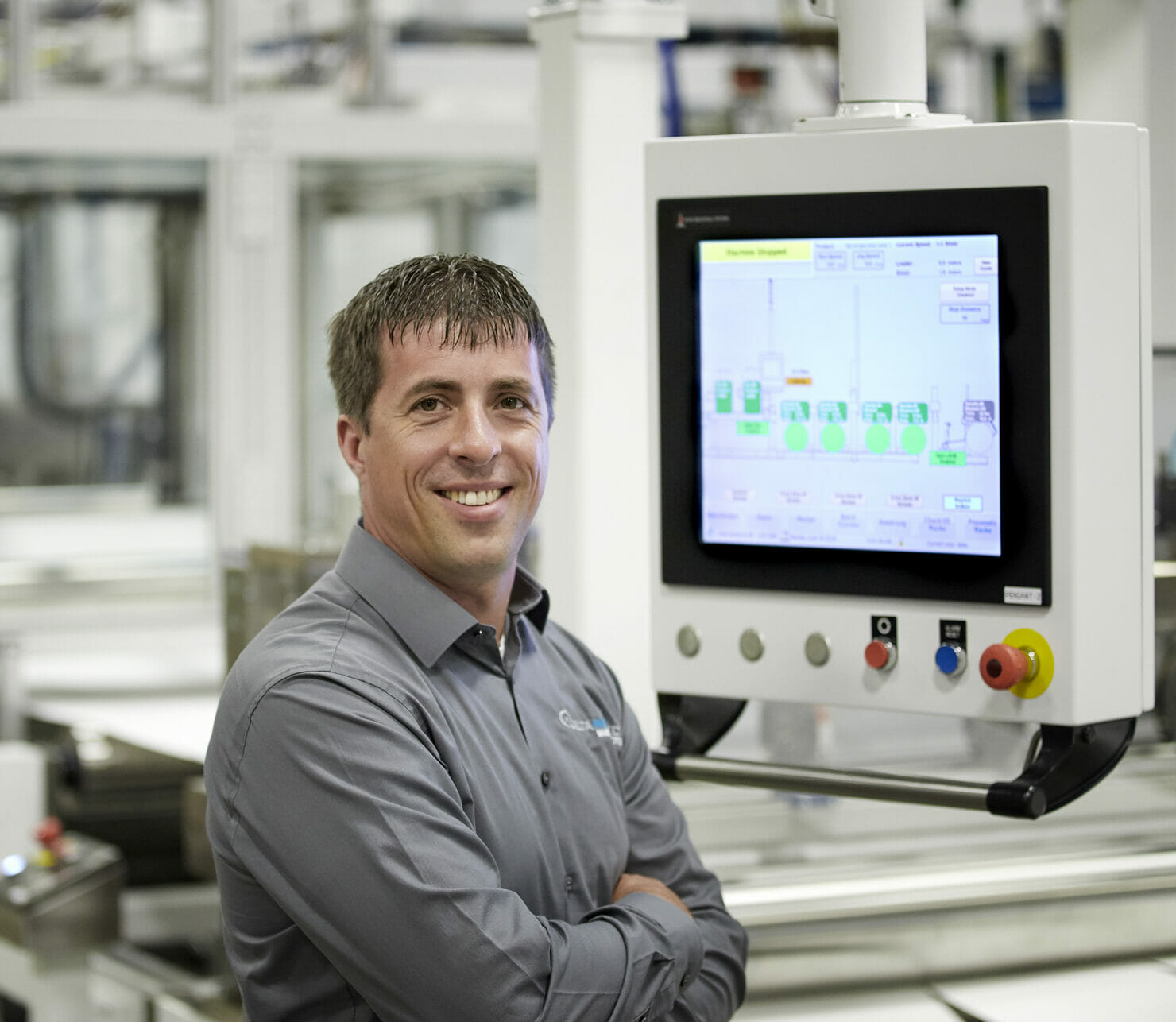
From curious questions to preparing a quote, we’re ready to help.
Whether we’re answering some introductory questions or if you’re in need of a quote, just fill in the form or call us at 1-800-279-3358 and we can get you the answers you need.