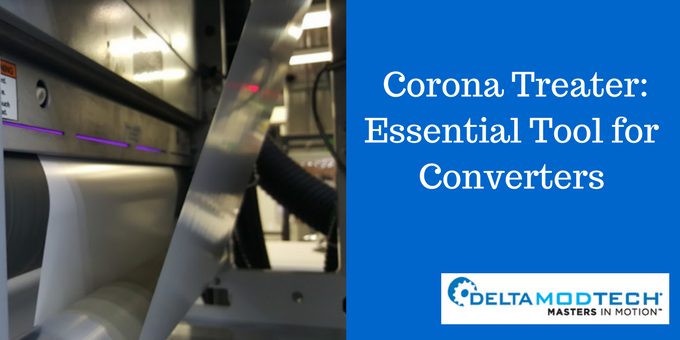
6 Ways Corona Treatment Can Improve Your Converting Operation
Todd Krupa is a sales representative from Enercon Industries. His focus is on selling corona treatment systems, a rather esoteric subject for people outside the industry.
“If I’m at a social event and I tell people what I do, they typically think I’m selling beer,” he laughs.
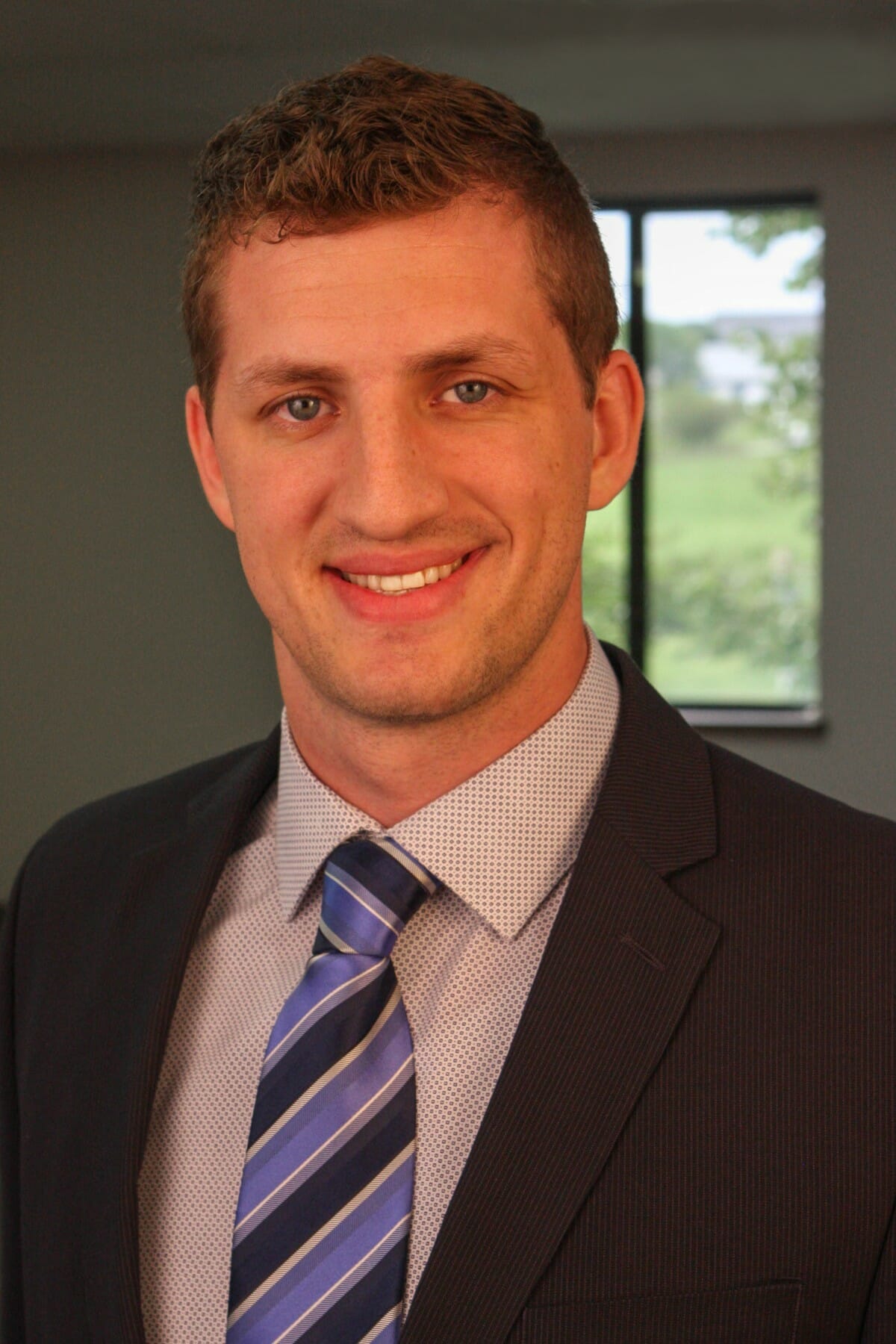
Todd Krupa, Enercon Industries
But a savvy converter is well aware of how corona treatment systems can impact their operation. By increasing the surface energy of films, foils and papers and improve the “wettability” and adhesion of inks, coatings and adhesives, a corona treatment system impacts everything from scrap to inventory control.
We turned to Enercon to provide us with further explanation of how corona systems works, and what they can do to help your converting output.
What is Corona Treatment?
As we explain corona treatment, let’s recall Todd’s social conundrum. “Corona” is not a beverage in our example; it’s technically ionized air.
The goal of the corona treater is to allow inks, coatings, adhesives and laminations to bond with substrates. It does this by ionizing the air above the substrate.

This in turn, forms low molecular weight on the film surface; oxidizes the film surface, and forms positive and negative sites by adding and deleting electrons. It rids the material of organic and inorganic contaminants that can interfere with adhesion, and can actually microscopically increase the surface area.
The corona treater is essentially an electrode, and it sits above the roll. When powered up, it receives 10,000 volts somewhere between 20 and 30 kilohertz, and electrically induces the air above the substrate. “It’s very visual,” Todd says. “It’s a purple-looking haze.”
The substrate, which typically has a non-reactive, non-porous surface, suddenly becomes much more receptive to bonding with inks and coatings. The corona treater essentially cleans the surface, and prepares it for adhesion and coating.
Here’s a video that shows how the corona treater works:
What Does the Corona Treater Look Like?
The corona treater includes an electrode, a grounded roll, a power supply, a transformer, and an exhaust duct.
The electrode sits above the grounded roll, where it creates the “purple haze.”
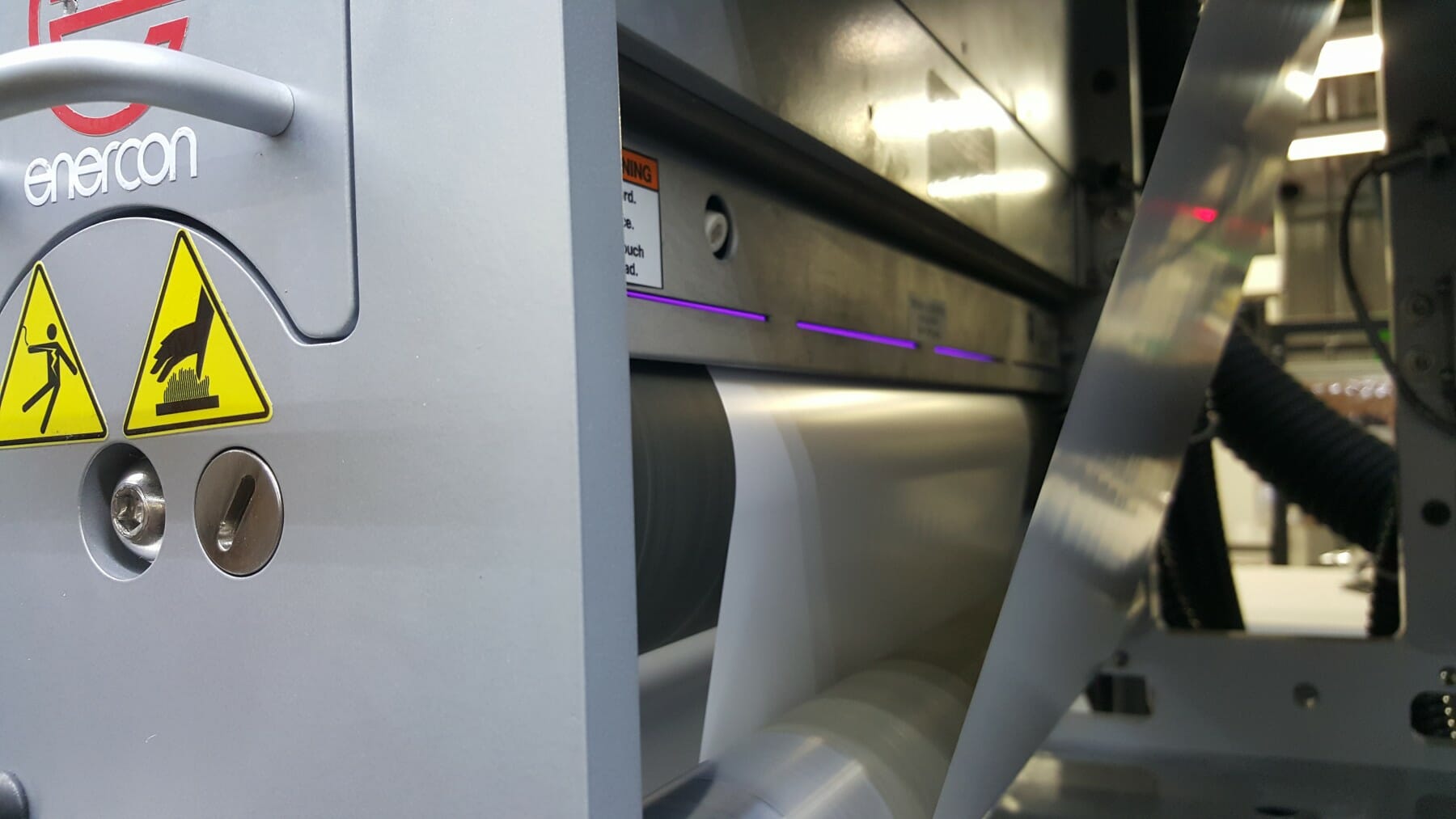
The power supply accepts standard utility electrical power and converts it into single-phase, higher-frequency power that is supplied to the treater station.

In this expert interview, Todd Krupa discusses the difference between the various types of ground rolls in the corona treatment system, and their applications.
Six Ways Corona Treatment can Improve Your End Product
So how can a corona system help you with your converting processes? Todd touched on six key benefits:
1. Cleans your materials
Surface contaminants interfere with adhesion. Dust, as well as additives that migrate to the surface of your materials, are forms of contamination. The corona treatment process cleans the material surface to promote adhesion.

2. Improves adhesion quality
By increasing the surface energy of your materials, you make it more receptive to bonding. Your materials will adhere and stand a far greater chance of passing the tape test.
3. Reduces wasted materials
When the adhesion process fails, wasted materials are created. Not to mention the lost production time. A corona treater provides insurance that your adhesion processes go as planned by eliminating surface energy as a variable.
If you have less errors, you have less scrap and a more efficient operation.
4. Reduces decayed surfaces of pre-treated materials
Some materials have been pretreated for your printing, coating and laminating operations. You may be able to use these materials without additional in-line treatment.
However, your dyne level (which is an indicator of your chance for adhesion success), over time can be affected by factors such as time, humidity, additives and contamination, as illustrated in the graphic below. “Bump treatment” returns the materials to their pretreated dyne levels.

5. Improves inventory flexibility
This ties in with bump treatment and decaying surfaces, but if you have a methodology for restoring dyne levels, then you don’t have to worry about the material sitting on your shelf. You’re effectively zapping the “expiration date.”
6. Overcomes migrating additives
Some materials may contain migrating additives. Additives perform useful functions such as reduce static; provide resistance to sunlight through UV stabilization; and act as slip agents to make film easier to handle through printing and coating processes.
Additives will migrate to the surface of the roll prior to adhesion. The substrate will then bond to the additives and not to the surface. Corona treatment blows those additives away.
Measuring the Results
Besides the tape test, which involves applying a piece of tape on the surface of the material and seeing if it picks up ink, a dyne pen or dyne solution is used to measure adhesion.
You might get an initial reading of 30 to 32 of the surface energy before the treatment, and then 42 after treatment. This is where the tweaking comes in — you’d need to run the job to see if the treatment resulted in the proper level of adhesion. It may require adjustments to the watt density (that’s how the surface treatment is measured).

Todd is quick to point out that corona treatment does not guarantee adhesion. “It’s not a magic box,” he said. These tweaks will help you find the right level at which to set the corona treater, but they will vary based on the materials.
“It all depends on the recipes you need,” Todd says. You may need to adjust the corona treatment based on the speed the press is running, the substrates you are using, the materials you are printing on. All factors need to be considered.
An Insurance Policy When the Stakes are High
In the converting world, efficiency and quality are a never-ending quest. The winners in this game find ways to minimize scrap and reduce errors.

That’s especially the case when you’re dealing with medical or pharmaceutical devices. These types of converting projects have extremely tight tolerances. End customers have zero tolerance for errors — the costs for failures are simply too high.
It’s really about risk management. And if you’re looking to mitigate risk and maximize profit, corona treatment is an insurance policy worthy of consideration.