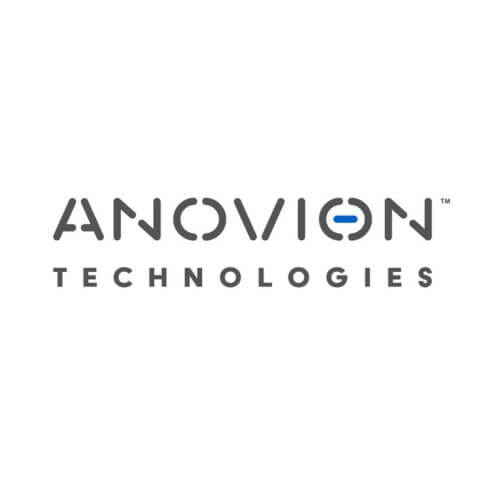
How Graphite Producer Anovion Technologies Meets the Real-World Coating Specs of Li-Ion Battery OEMs

How does a company that produces synthetic graphite for lithium ion batteries ensure its product is manufacturer-friendly? For Anovion Technologies, the key was to replicate the manufacturing processes – and challenges – of its OEM customers.
But to do that, the company needed an exceptional slot-die coating machine and the technical support to implement it effectively.
Challenge
To say Anovion is a one-of-a-kind company is true in multiple ways. For example, it was one of the first 100% domestic commercial producers of synthetic graphite for lithium ion (Li-ion) batteries.
And thanks to a highly streamlined proprietary process, the company has cut the number of steps by about half compared to the typical graphite production process. This not only reduces its energy consumption and carbon emissions but also expedites the graphite’s speed to market.
Then there’s Anovion’s unique – and proprietary – graphite formulation, which enables a long life cycle.
However, none of these impressive factors would matter unless potential OEM battery customers can effectively use the graphite in their battery manufacturing.
You need to show an OEM that your product works
Each OEM has a specific set of requirements for its end products, and the process and formula for synthetic graphite anode material must be adjusted accordingly to align with its expectations. This typically occurs in a specialized testing process to demonstrate graphite performance.
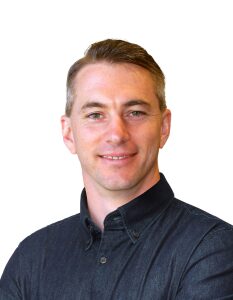
According to Jeremy Schrooten, PhD, Vice President of Anovion Technologies, “It is critical to bring data to a potential customer that shows the benefits our products can provide. To do this, Anovion built an internal state-of-the-art battery lab that uses the same processes as large manufacturers, but at small scale. This forces Anovion to experience all the issues and challenges the customer would experience, and then be prepared with a solution.”
To accomplish this, Anovion needed the same high-grade equipment as its OEM battery customers. And one machine in particular was at the top of the list.
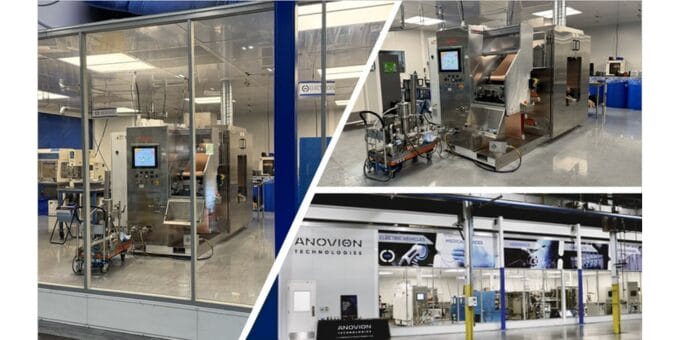
Solution
“Every major battery manufacturer out there uses a slot-die coater as their preferred coating technology to make electrodes,” says Jeremy. “So, from the start, that’s what we wanted.”
While most battery labs would likely balk at the expense of a slot-die coater, Jeremy knew just how critical the machine was for understanding customer needs and elevating the company’s ability to meet them.
Ultimately, he and his team chose the DynaCoat® slot-die coater from Delta ModTech, a decision that has brought far-reaching benefits like the following:
“Flawless” performance and reliability. Developing a lab required sourcing – and integrating – equipment from a variety of vendors, a process not without its challenges. According to Jeremy, they initially had issues “with basically everything except the slot-die coater.”
Today, after subsequent equipment upgrades and process improvements, he says Anovion can make “world-class” batteries. “But the Delta coater has been a flawless machine for us from the very beginning.”
Flexible, ongoing technical support. Jeremy also says Delta ModTech’s continuing engagement with the Anovion lab has played a pivotal role in using the DynaCoat machine as effectively as possible.
“Whether it’s been live remote help to work through a specific challenge or onsite support to help us optimize the coater’s performance, Delta has been there for us whenever we’ve needed them.”
“Process experts” to help improve coating quality. Of course, machine expertise is important, but Jeremy notes that Delta ModTech’s support goes further.
Delta understands the trade-offs between the coater parameters and the slurry parameters. They’ve given us insights for making adjustments to both so the two work better together. They’re not just machine experts – they’re also process experts.
Jeremy Schrooten, PhD, Vice President of Anovion Technologies
Throughput
With the help of Delta ModTech, Anovion can do more than replicate Li-ion battery production in-house. By testing its graphite in real-world production scenarios, the company can provide customers with both outstanding service and a superior final product.
Customer-centric battery production. To test the performance of their graphite, Jeremy and his team didn’t want to be limited to coin cell technology, a fairly inexpensive, industry-wide practice that uses batteries similar to those found in watches and garage door openers.
“Coin cells are not representative of what our customers have to deal with,” he says, “which is why we wanted to take our testing capabilities to the next level.”
Anovion can indeed carry out next-level testing today because it can produce standard batteries like the 18650 cylindrical format battery, which is commonly used in electric vehicles.
A highly informative, easy-to-grasp data package. Anovion’s in-house coating technology gives Jeremy and his team an evaluation platform for thoroughly understanding a given slurry’s properties, requirements, and metrics. But more than that, it empowers them to anticipate customer questions and provide truly valuable information.
“We can give customers a highly detailed data package so they can see everything we’ve done to evaluate the graphite,” says Jeremy. “They don’t have to try and figure it out for themselves.”
More credibility and deeper customer engagement. According to Jeremy, “By testing graphite using industry-relevant batteries, Anovion is able to partner with cell producers to ensure our products meet their expectations.”
Establishing a firm hold as Li-ion battery technology flourishes
With the era of the Li-ion battery clearly upon us, Anovion is poised to be an integral part of it. The company has announced plans for a 1,200,000-square-foot manufacturing facility in Southwest Georgia, which is expected to produce 40,000 metric tonnes of synthetic graphite per year and create hundreds of clean energy jobs in the process.
In the midst of these exciting changes, Anovion’s in-house graphite-testing capabilities will continue to be a key part of the company’s approach.
“Electrode coating is a critical step in the production of a battery, and having Delta ModTech as our partner amplifies our success in delivering a world-class product to the marketplace,” explains Jeremy. “Based on my experience with Delta, I’ve never hesitated to recommend them as a partner for coating solutions.”
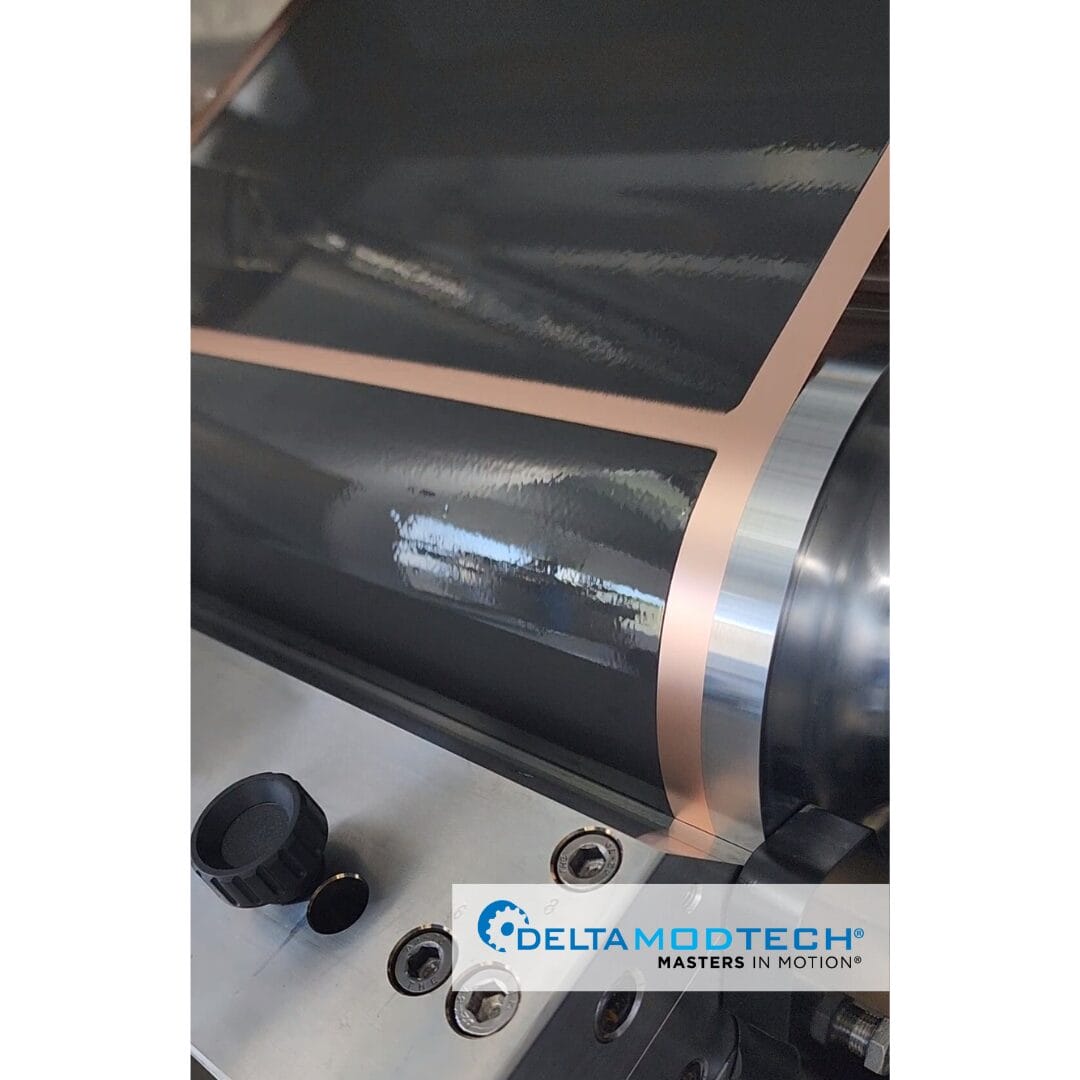
About Delta ModTech and Battery Manufacturing
To better understand how Delta ModTech can help you, check out this additional information on our battery manufacturing capabilities.
Choose the right methodology for your next coating project.
Published on Aug 01 2024
Categories: Case Studies
Previous Post
Label Expo Americas