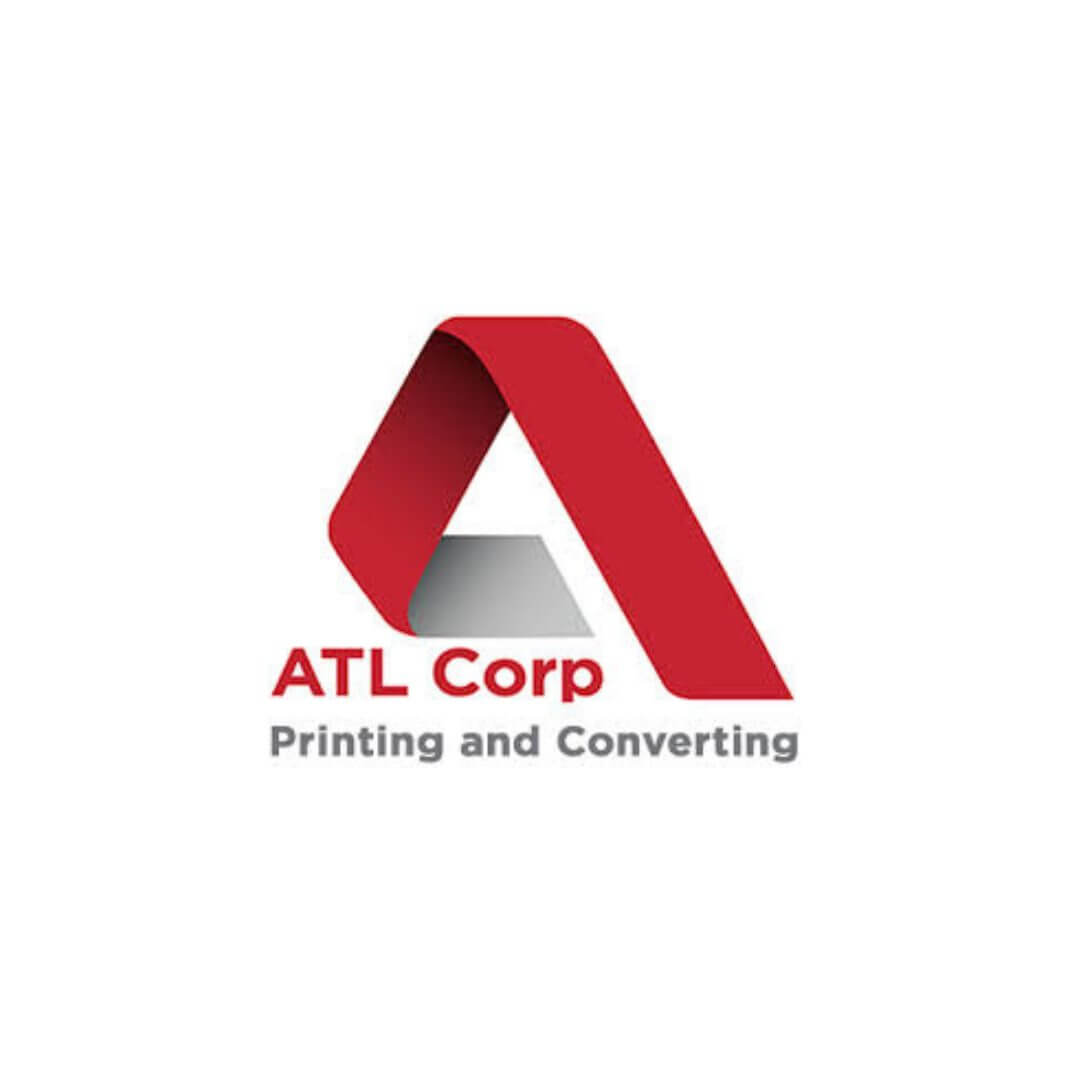
From Concept to Mass Production: ATL Corp. Produces a Breakthrough New Medical Device Product Through Collaborative Innovation with Delta ModTech
ATL specializes in flexographic and digital printing, material converting, and contract manufacturing. They manufacture custom converted parts, using medical grade tapes and foams.
Based in Menomonee Falls, WI, the company first began by printing labels in 1954. Eventually, their capabilities expanded to flexographic and digital printing, die cutting, laminating and contract manufacturing.
For many years they had been doing some converting and die cutting projects on Mark Andy brand flexographic presses, but it wasn’t until they bought their first Delta ModTech machine that they began to take on more advanced projects, such as laminating, island-placement and cold-seal packaging.
“We’ve been a longtime partner of Delta ModTech,” said Jason Hynes, Vice-President at ATL.
The years of partnership prepared ATL for the day when a start-up medical company named KelCor approached them with a new product concept.
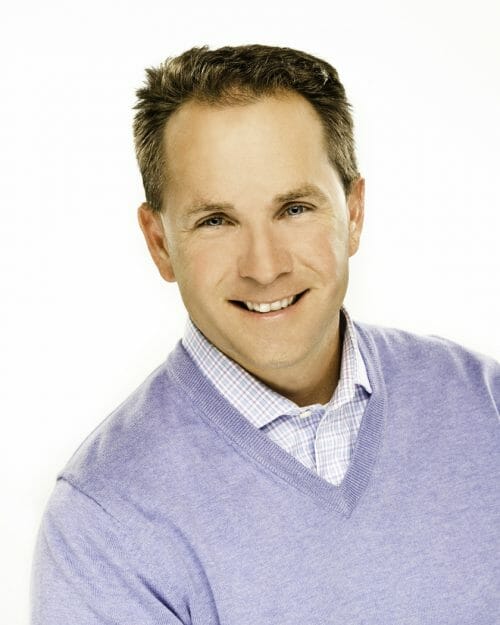
Challenge: Developing a medical device prototype for KelCor
When a patient is intubated, surgical tape is used to secure the airway tube through a standard methodology. That tape, called a drape support, can be subject to airborne particulates and splash, and as a result may become a potential source of healthcare-acquired infections.
KelCor wanted to remove the risk of healthcare-acquired infections by producing a single-use adhesive piece that could be removed from sterilized packaging. In addition, KelCor wanted to include eye coverings — applied by the anesthesiologist when the patient is sedated — in the packaging.
With the input of other medical practitioners, KelCor developed a general concept of the securing device, but it needed a methodology to manufacture the packaged product in a cost-effective manner and in adherence to regulatory guidelines. They turned to ATL.
Want to see your business’s success story featured on our website?
Solution: Relying on the multiple capabilities of the Delta ModTech Crusader
ATL worked with KelCor to create a prototype of the securing device. The drape support product was a die cut, multi-layer lamination with adhesive. ATL turned to its Delta ModTech Crusader converting machine to produce it.
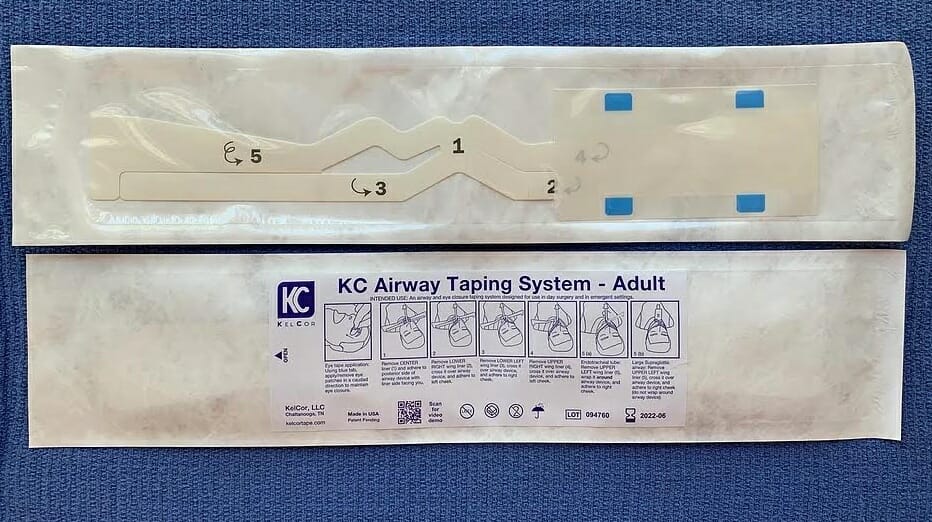
“Delta’s machines are servo driven, so they have very tight registration of the die cut controls,” Jason said. “The contour of the part required precise die cut and registration. Because there are multiple materials involved, it required specialized converting equipment to fabricate the product.”
The eye patches were also produced on the Crusader. The patches and the securing device were then kitted together and hot-sealed into custom packaging. “We were able to convert it, package it and ship it to a sterilization company,” Jason said.
Throughput: Bringing the New Product to Market
Once the prototype proved viable, ATL was able to produce the first 5,000 part order. Now the ball is in KelCor’s court, as they work to distribute the product and change behavior of how nurse anesthetists use the product.
KelCor believes the superior design of the product and its ease of use will lead to medical practitioners switching to the new approach. The enhanced attention to disinfecting as a result of COVID-19 will only boost its appeal.
Unlike many Delta ModTech projects, this one didn’t require our direct involvement in the development of the prototype with ATL. That’s a testament not only to their engineering acumen, but to the training and support Delta ModTech has provided to them over the years. They know how to use the Crusader to convert a vision into reality.
“Delta ModTech has always provided tremendous support for us, so when we take on a big challenge, we’re always ready to roll,” Jason said. “But it’s good to know if we need them, they’re there.”