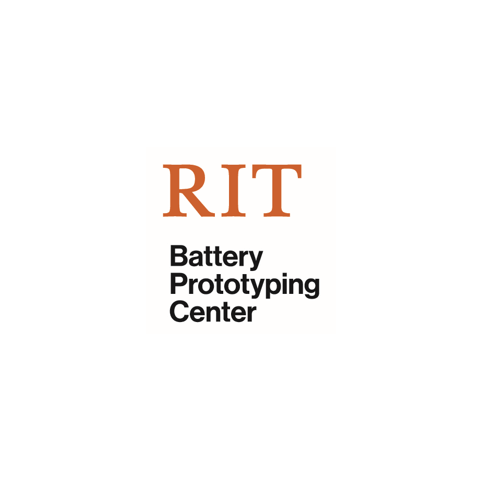
Battery Lab Becomes Invaluable Industry Resource by Adding a Scalable Coating Line
It was created to “help companies develop the next generation of battery materials,” said Dr. Matthew Ganter, Director of the Battery Protyping Center at RIT (Rochester Institute of Technology).
The center focuses on the development of emerging storage technologies, working with manufacturers, material developers, universities and other national labs to test new battery design in a commercial-quality form factor.
“We handle the testing characterization for them, so companies don’t have to invest large capital funds to create prototypes, pilot-scale demos,” Ganter said.
The companies can then use the results to modify their product, or share it with investors to secure more funding. But replicating that commercial-quality form requires the right equipment, and for that, BPC needed help.
Challenge: Missing a critical piece of the manufacturing process
The RIT Battery Prototyping Center’s initial funding allowed for the construction of a dry room and some equipment. But it lacked a small-scale slurry mixing and coating line, and relied on partners for their roll coating capabilities. But the lack of coating equipment soon became a problem.
“We could only coat on a meter-long sheet at a time, with small batches of battery slurry,” Ganter said. The inability to scale was stretching the center’s ability to keep up with the demand.
The center needed a mixing and coating line with roll to roll capabilities. It required a machine that could be customized to fit in limited space, and also be moisture sensitive to the dry room environment.
Solution: A customized coating line that allowed BPC to scale
After securing additional funding for the coating line, the RIT Battery Prototyping Center reached out to a number of vendors for a bid, including Frontier, a Delta ModTech company. Frontier designed a custom system that provided:
- Flexibility: Frontier’s customized machine allowed for mixing, coating and slitting capabilities. It also had two different coating heads, which allowed BPC to switch between slot die and knife-over-roll.
- Customized footprint: The machine was custom built to match the dimensions of the dry room setting. It did not require a separate power source, reducing retrofitting costs for the lab.
- Accuracy: The machine allowed for tight tolerances and percentages. It also included a displacement pump system, which delivers fluid accurately to the slot die.
Throughput: An enhanced impact on the industry
The purpose for the RIT Battery Prototyping Center is to be a resource to the battery industry; a partner to help companies get from A to B in the most efficient way possible. RIT Battery Prototyping Center’s selection of Frontier resulted in a similar type of relationship.
“We weren’t just buying equipment,” Ganter said. “We wanted a partner we were comfortable working with — someone who could help us enhance their impact on the industry,” Dr. Ganter said.
Besides providing ongoing consultation on the machine’s operation, Frontier participates and sponsors the RIT Battery Prototyping Center’s training events, sharing their coating expertise with battery innovators worldwide.
“It’s nice to have that personal relationship and a one-stop shop,” Ganter said. “It’s been a good partnership.”
OVERCOME YOUR BIGGEST CONVERTING AND PACKAGING CHALLENGES
Published on Oct 09 2020
Categories: Case Studies