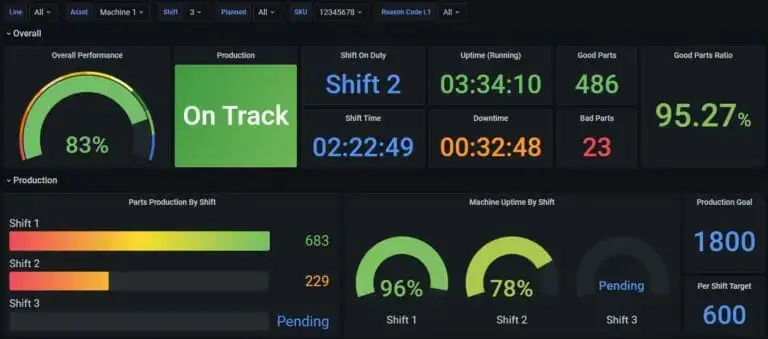
How Coaters and Converters Can Use Data to Drive Better Performance
Your production machines can be an invaluable source of data—but are you capturing the metrics that matter? Relying on outdated logs, scattered reports, and incomplete tracking can leave you blind to inefficiencies and unable to make meaningful improvements.
Ideally, you should designate the metrics critical to your operation and then implement a system that automatically captures them. “When you can do that, things like tracking efficiency, reducing waste, and improving uptime become much more possible,” says Todd Kruse, a Delta ModTech electrical engineer with nearly 25 years of experience.
In this post, we’ll first break down the key metrics that can help transform your production performance. We’ll then introduce ModTech CONNECT™, a powerful new tool that can dramatically improve your data collection—and ultimately help transform your long-term performance.
Leverage performance data to improve efficiency and quality
For manufacturers to outpace their competition, having immediate visibility into machine performance is no longer a luxury—it’s essential. Real-time tracking and historical data analysis can provide insights into crucial production areas like the following.
“Every time a machine stops, you should be able to know exactly why.”
Todd Kruse, Electrical Engineer, Delta ModTech
Uptime and downtime tracking
How can you systematically find ways to minimize production disruptions? Without real-time tracking, it can be a struggle to pinpoint the causes behind stoppages. Meanwhile, potential areas for improvement continue to be missed.
“Every time a machine stops,” says Kruse, “you should be able to know exactly why. Was it a designated break or lunch? Was it a material change, or a process change to a different product altogether?”
When you have a system to track downtime, you can take proactive steps like these:
- Identify and log all stoppage reasons
- Reduce changeover delays through improved setup procedures
- Optimize machine scheduling to minimize downtime

Material usage and waste reduction
Material waste can be one of the biggest drains on profitability. In industries like batteries and medical devices in particular—where raw materials come at a premium—even small inefficiencies can lead to significant cost overruns and excessive waste.
“For some manufacturers, it’s all about the material,” says Kruse. “So cutting down your startup times, your changeover times, and improving the efficiency of your yields is critical.”
When you can track material usage down to the precise unit, you’re in a much better position to carry out specific strategies such as:
- Monitoring material yield rates to reduce unnecessary waste
- Refining coating or converting techniques for better resource utilization
- Optimizing startup and changeover times to minimize material loss
“Tracking at the shift level as well as the operator level can help you make better decisions on training, process improvements, and machine utilization.”
Todd Kruse, Electrical Engineer, Delta ModTech
Operator and shift performance monitoringProduction output can fluctuate between shifts due to variations in operator efficiency, adherence to procedures, and machine settings. But without clear performance tracking, it’s difficult to truly understand the inconsistencies or uncover areas for improvement.
“How well is an operator running a machine? Tracking at the shift level as well as the operator level can help you make better decisions on training, process improvements, and machine utilization,” says Kruse.
With real-time operator performance tracking, you can help ensure greater consistency across shifts and find opportunities for improvement. Here are just a few examples:
- Identify training gaps to improve operator efficiency
- Standardize best practices across shifts for more consistent output
- Analyze shift performance trends to optimize scheduling and labor allocation
“If a recall happens, you want to know exactly what materials were used and where.”
Todd Kruse, Electrical Engineer, Delta ModTech
Production tracking and traceability
In industries requiring stringent compliance and traceability, a lack of real-time production tracking can have dire consequences.
“Take pharmaceuticals for example. Tracking every component is critical. So, if a recall happens, you want to know exactly what materials were used and where,” says Kruse.
In fact, real-time tracking can not only help strengthen compliance but also improve efficiency and enhance quality assurance by enabling you to:
- Pinpoint defects early by tracking tooling wear, calibration issues, and material inconsistencies (see the next section for related info on this point)
- Ensure complete traceability with barcode scanning and digital recordkeeping
- Improve first-pass yield by diagnosing and correcting process inefficiencies in real time
Go from reactive to proactive with predictive maintenance data
While production data can help optimize efficiency and provide deep insights into performance, you also want to track maintenance-specific metrics that, among other benefits, signal when servicing is needed.
“On some coating lines, for instance, manufacturers start noticing streaks, bubbles, things like that occurring. But tracking machine wear can help predict when a tool should be changed. Now you can prevent a problem before it shows up in the product,” says Kruse.
By tracking maintenance indicators, you can shift from reactive fixes to proactive servicing. In the process you’re also extending equipment life, improving product quality, and maintaining smoother production. Specific examples include:
- Tracking tooling wear such as die life and blade sharpness
- Scheduling service based on cycle counts and actual machine use (not guesswork)
- Detecting process deviations like incorrect pressure settings or over-tightened dies
How to put real-time machine data at your fingertips
As you’ve just seen, the right metrics can indeed drive improvements—but you have to capture those metrics first. Unfortunately, many data collection solutions are generic, off-the-shelf systems. That means they don’t account for the unique needs of coating and converting manufacturers.
That’s why Delta ModTech developed ModTech CONNECT™.
“We built ModTech CONNECT™ specifically for manufacturers—ensuring it works with their machines, their processes, and their production goals,” explains Kruse. “It’s also fully customizable, so users can focus on the specific metrics that matter most to them.”
With this system, manufacturers can:
- Seamlessly integrate machine data with MES and ERP systems
- Customize dashboards to specific users (e.g., operators, supervisors, managers)
- Track machine performance in real time to maximize uptime
- Access insights from any device—desktop, tablet, or smartphone
- Easily scale from one machine to a full production line
Exceptional tech support
Access to critical data can be a game-changer—when you know how to use it. That’s why Delta backs ModTech CONNECT™ with ongoing service and support, helping you to not only collect metrics but apply them for lasting improvements.
Are you ready to unleash the power of your machine metrics?
In today’s fast-moving manufacturing world, more and more industry leaders are using real-time machine data to push performance limits, reduce downtime, and eliminate waste. ModTech CONNECT™ provides easy access to information that can ultimately transform your operations.
To start a conversation and learn more about ModTech CONNECT™, be sure to call us at 1-763-755-7744 or fill out our online form to get started!
OVERCOME YOUR BIGGEST CONVERTING AND PACKAGING CHALLENGES
Published on Apr 17 2025
Last Updated on Jul 09 2025
Categories: Delta ModTech Blog, Reducing Scrap, Uptime
Next Post
Delta ModTech’s 2025 Technology Showcase
Previous Post
Converters Expo